[youtube]http://www.youtube.com/watch?v=SPdDGMuR04A[/youtube]
เห็นบางคนไม่ค่อยเข้าใจเรื่องเกี่ยวกับการฉีดพลาสติก เลยจะมาอธิบายเกี่ยวกับการทำพลาสติกโมเดลแบบคร่าวๆ
ซึ่งขั้นตอนแบบทั่วๆไปจะแบ่งขั้นตอนคร่าวๆออกเป็นสเตปต่างๆดังนี้
1. วางแผนการผลิต
2. ออกแบบรูปทรง 3D
3. ออกแบบการวางชิ้นส่วนต่างๆ
4. เริ่มทำตัวโปรโตไทป์ต้นแบบ
5. เริ่มทำการผลิตแม่พิมพ์
6. เริ่มทดลองฉีดงาน
7. ตรวจสอบระบบการผลิต
8. ทำการวางขาย
ว่ากันตามขั้นๆทั่วไป
1. เริ่มวางแผนการผลิต
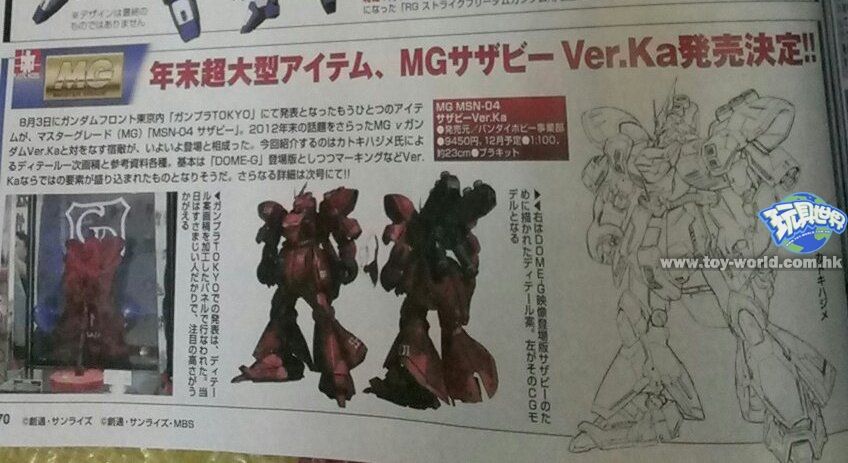
นั่นก็คือเริ่มวางแผนการณ์ว่าจะขายเมื่อใหร่ วางกดหนดช่วงระยะเวลาต่างๆ
2. เริ่มวาด CAD 3D
ในการดีไซนน์สมัยใหม่มักใช้ CAD 3D เป็นหลักในการออกแบบ โดยการปั้นรูปทรงในแบบ 3D ตามที่ต้องการ ก่อนที่จะไปขั้นตอนการออกแบบต่อไป
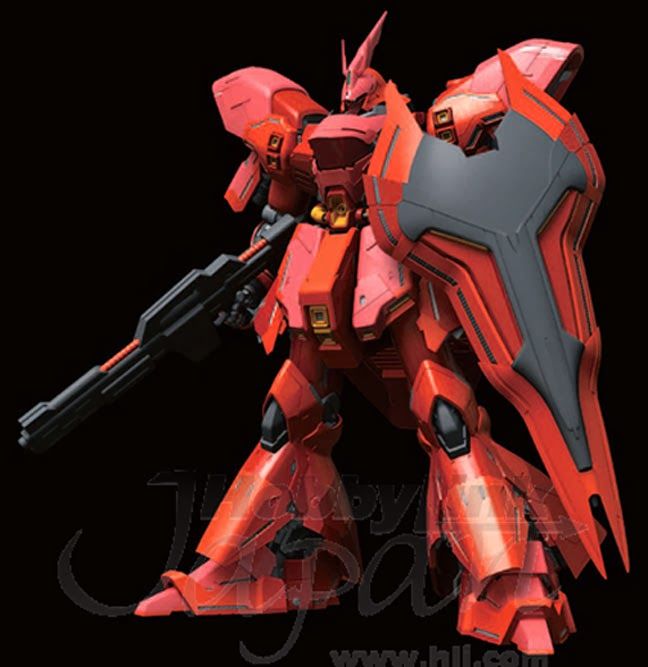
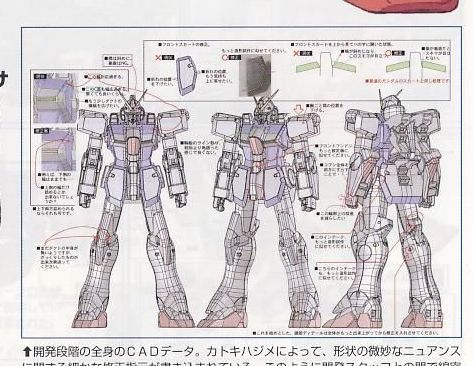
3. เริ่มทำการออกแบบโครงสร้าง การแยกชิ้นส่วนต่างๆ
เพราะการออกแบบด้วย CAD 3D นั้น ในขั้นตอนนี้สำคัญที่สุด เพราะถ้าขึ้นแม่พิมพ์เหล็กไปแล้วจะทำอะไรก็ยาก
สำหรับโปรมแกรมที่พอรู้จักก็ได้แก่ NX และ Solid work อต่เอาจริงๆโปรแกรมพวกนี้มีเยอะมาก ตามแต่บริษัทจะซื้อมาใช้กัน
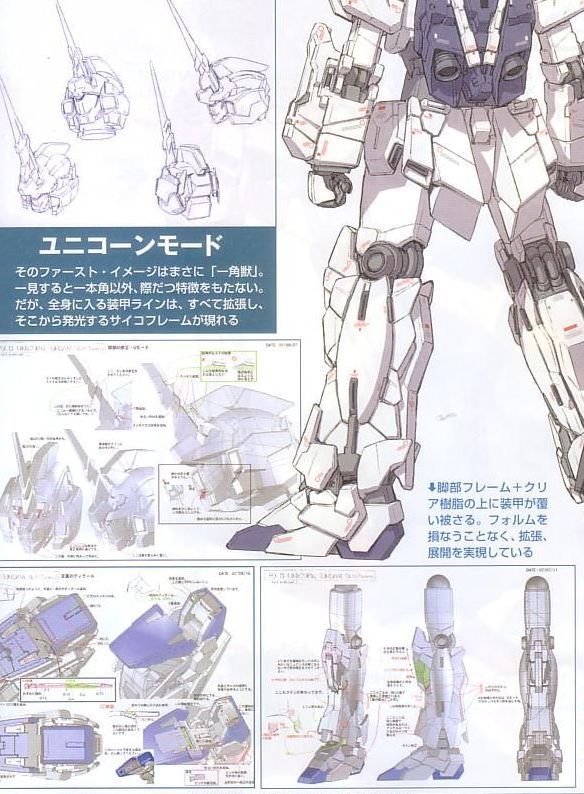
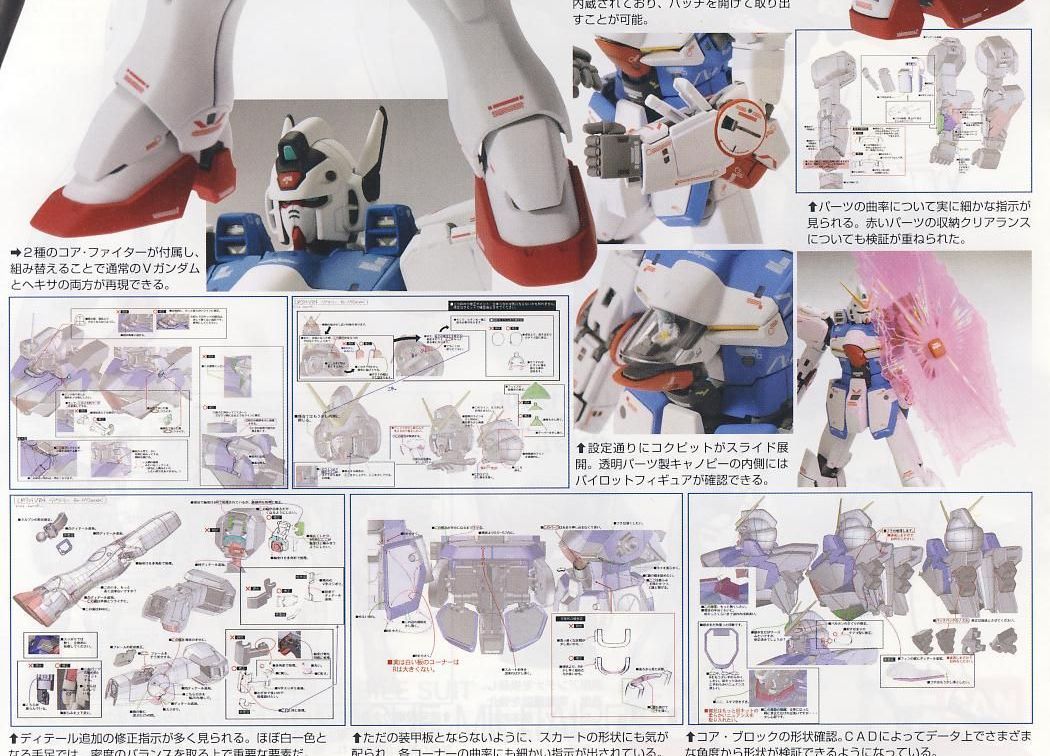
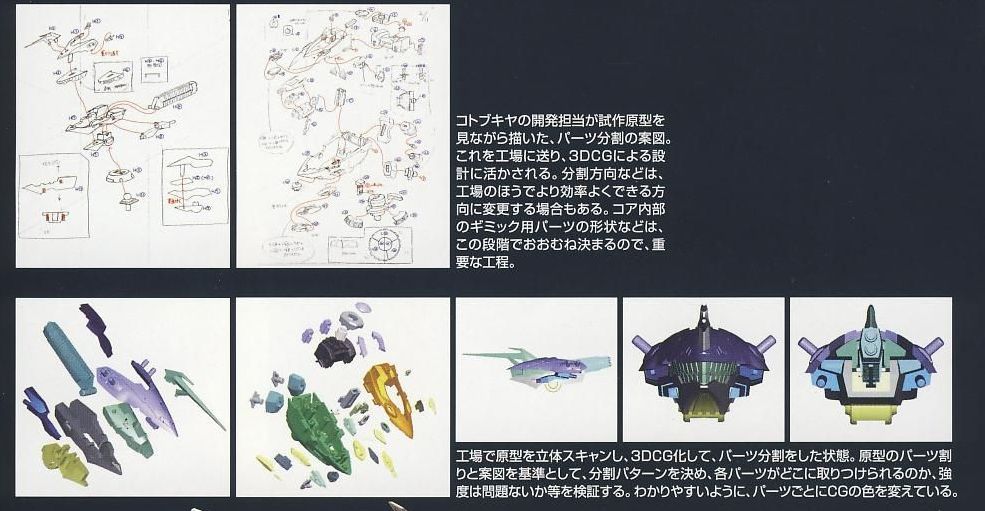
4. เริ่มทำโปรโตไทป์ต้นแบบ
เพราะแม่พิมพ์เหล็กนั้นแพงมาก จึงมักมีการสร้างตัวต้นแบบคร่าวๆขึ้นมาก่อนเพื่อเช็คการดีไซนน์ต่างๆ
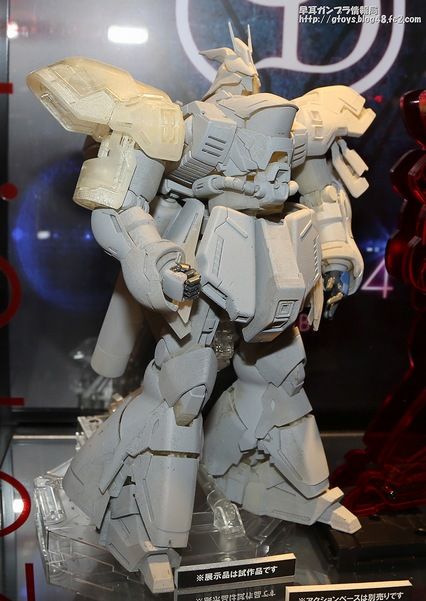
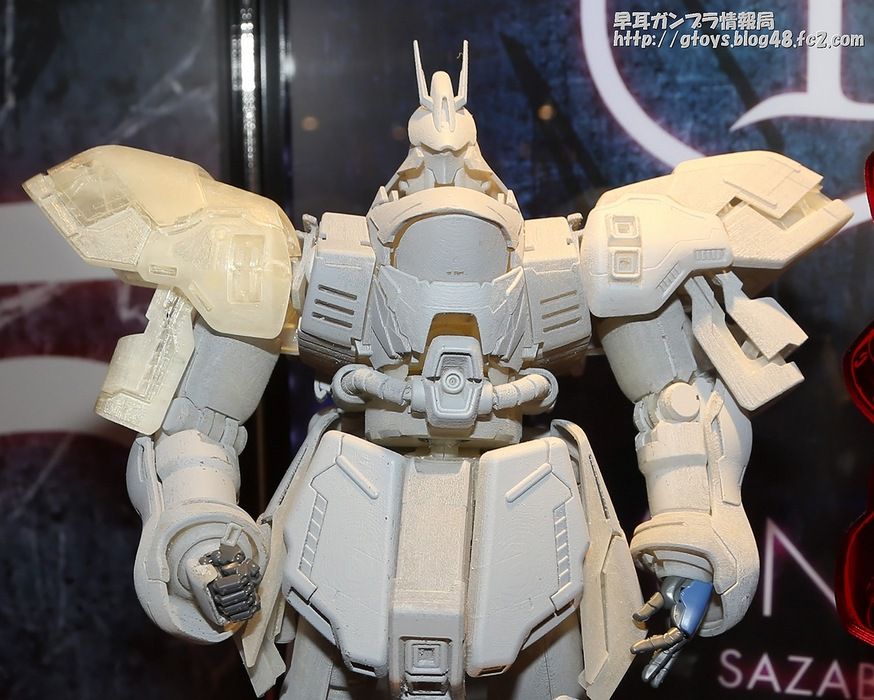
สำหรับพวกโปรโตไทป์จะเห็นว่า ผิวมักจะสาก บางทีก็เป็นลายๆ และมักจะสีใส ถ้าเป็นอย่างนี้มักจะเกิดจากเครื่องทำเรปิดโปรโตไทป์แบบทั่วไป
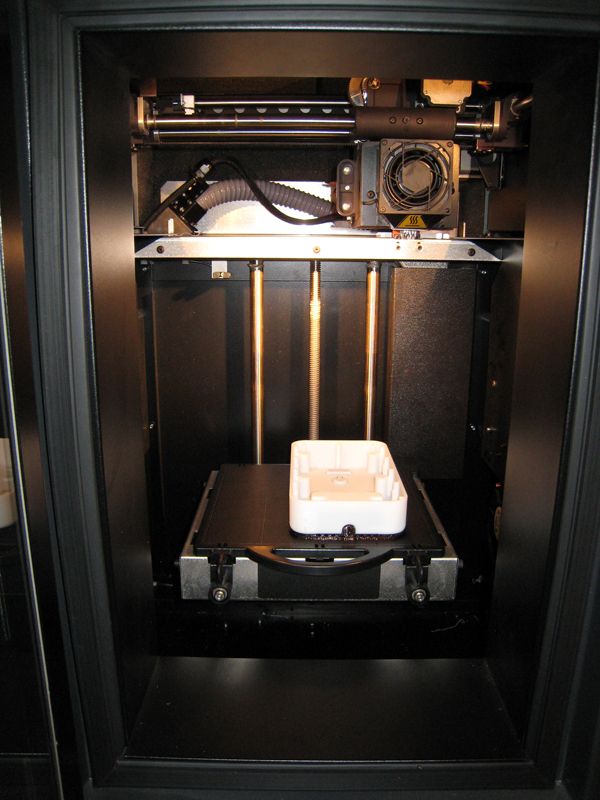
ทำหรับเครื่องเรปิด โปรโตไทป์ จะใช้หลักการของการฉีดพลาสติกแบบเป้นชั้นๆ คือ จะคล้ายๆเครื่องปริ้น แต่ฉีดพลาสติกออกมาตามความหนาของหัวฉีดพลาสติก และค่อยๆฉีดทับๆกันเป็นชั้นๆ หรือเรเยอร์
ทำให้ตัวโปรโตไทป์ต้นแบบของงานกันพลาที่เราเห็นมักเห็นเป็นลายชั้นๆ
ซึ่งความคมชัดขึ้นอยู่กับหัวฉีดของเครื่องโปรโตไทป์เป็นหลัก เช่น ถ้าหัว 0.3มิล จะฉีดพลาสติกได้ชั้นละ 0.3 มิล พวกดีเทลที่หนา 0.1 มิล จะไม่สามารถทำได้ หรือหายไปเลย เป็นต้น
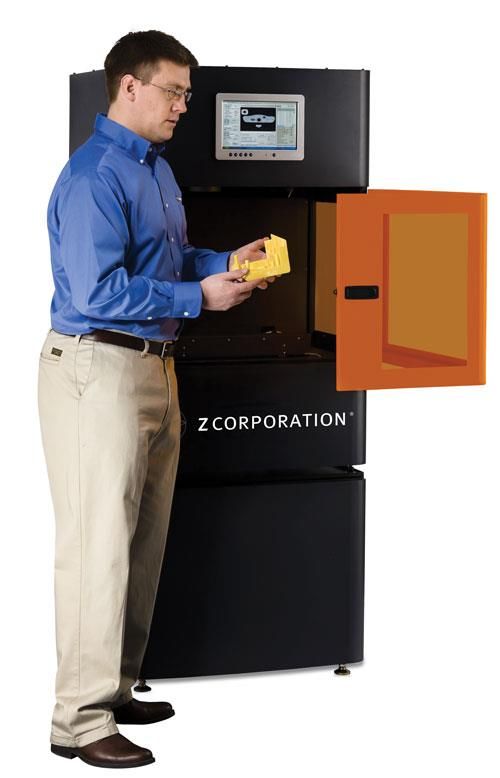
ซึ่งงาน เรปิด โปรโตไทป์พวกนี้ ข้อดีคือถูก (แต่ถ้าเทียบกับเงินในกระเป๋าเราๆท่านๆก็ยังแพงนะ) บ้านเรามีบริษัทรับจ้างอยู่ แต่ชิ้นเล็กๆก็ราคาหลักพันแล้ว ใครคิดจะซื้อไปทำกันพลาออริจินอลนี่เลิกคิดได้เลยเพราะโปรโตไทป์พวกนี้เปราะมาก เนื่องจากเป็นการฉีดพลาสติกเป้นชั้นๆซ้อนกัน การเชื่อมต่อระหว่างชั้นเลยหลวมๆ ทำให้ตามรอยต่อนั้นแตกง่ายมาก
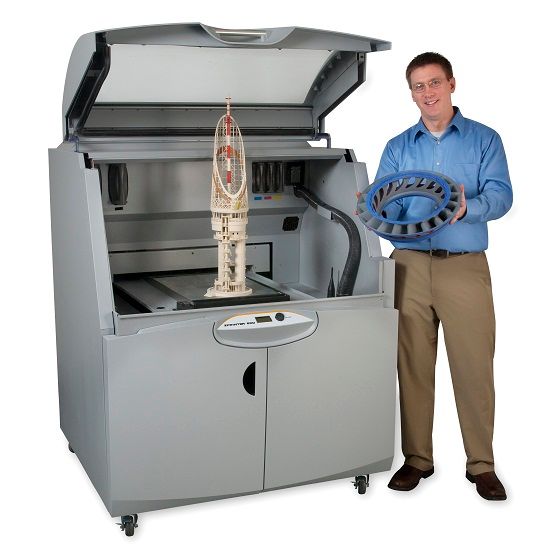
ซึ่งเทคโนโลยีสมัยใหม่นี้ เราสามารถทำ ปรินเตอร์ 3D ได้แล้ว แต่ราคาก็พุ่งขึ้นไปอีก
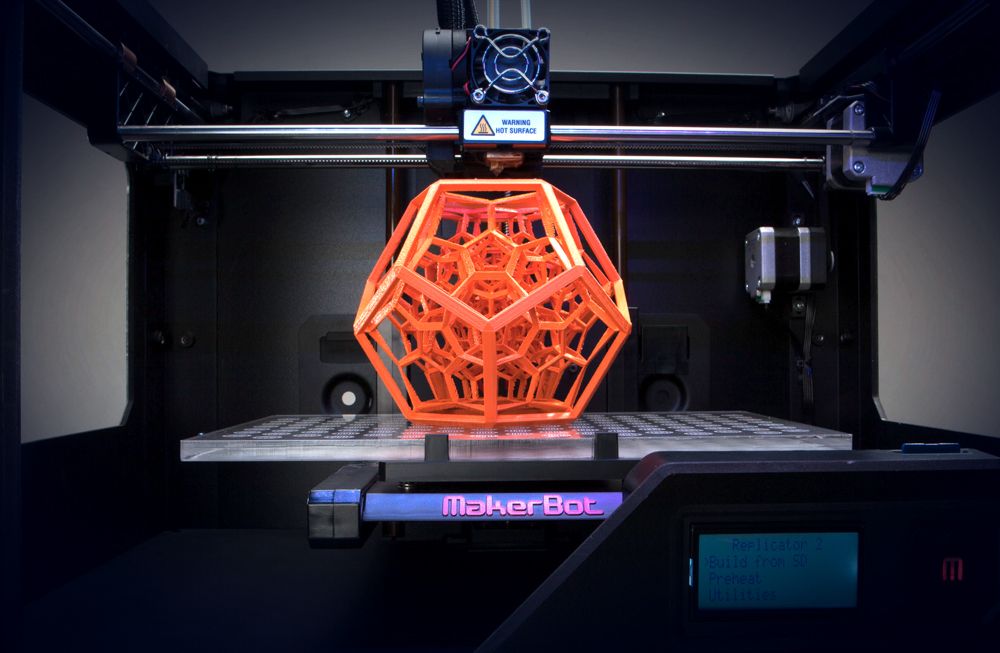
5. เริ่มทำการผลิตแม่พิมพ์
ทำการผลิตแม่พิมพ์ตาม 3D ต้นแบบที่ส่งไป ซึ่งวิธีการนั้นก็ไม่ง่าย เพราะถ้าทำมั่วๆซั่วๆ มักจะฉีดออกมาแล้วมีปัญหามาก สมัยใหม่เราเลยมักใช้โปรแกรมคำนวนการใหลของพลาสติกเพื่อจำลองการทำงานในขั้นตอน แมสโปรดักชั่น เพื่อลดความผิดพลาดที่จะเกิดขึ้นในอนาคต
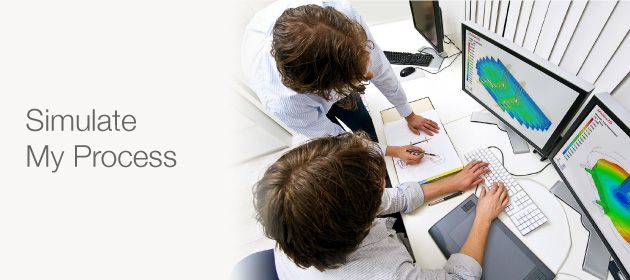
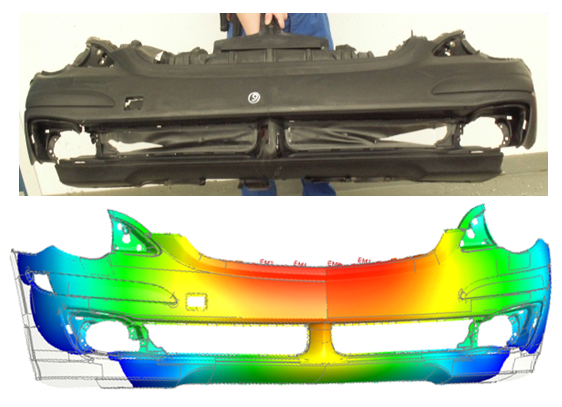
ซึ่งส่วนใหญ่ จะใช้โปรแกรมจำลองการใหลของพลาสติกเพื่อเช็คการออกแบบแม่พิมพ์เพื่อลดปัญหาที่อาจจะเกิดในอนาคตให้มากที่สุด
สำหรับการออกแบบแม่พิมพ์ก็ใช้แกรมแกรมเช่นเดียวกัน เพื่อจำลองการทำงานของแม่พิมพ์ขณะทำงานจริงๆ
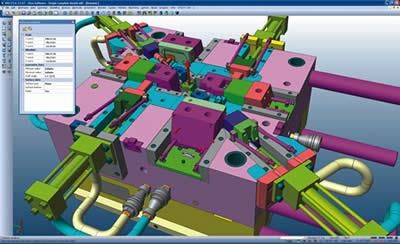
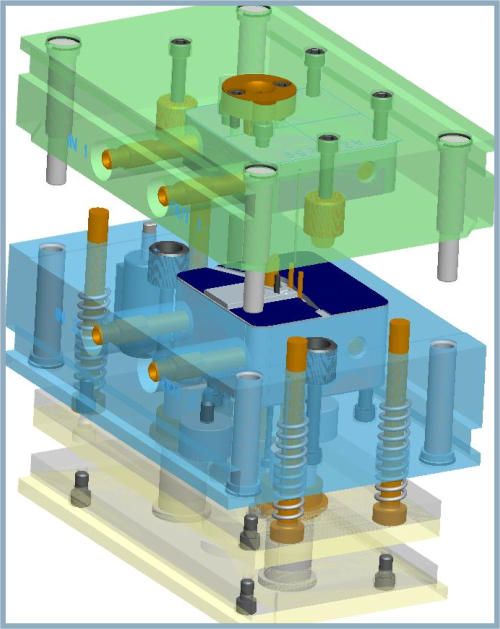
ซึ่งสำหรับโครงสร้างของแม่พิมพ์หลักการง่ายๆทั่วไปคือจะมีซีกบนกับซีกล่าง ส่วนบนที่เป็นผิวงานจริงๆจะเรียกว่า Cavity และส่วนล่างจะเรียกว่า Core
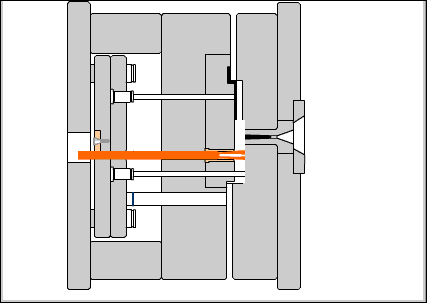
ซึ่งหลักการพื้นฐานง่ายๆคือ ซีกบนทับซีกล่าง ฉีดพลาสติกเข้าไป แล้วใช้ Ejector pin ดีดให้ชิ้นส่วนกระเด็นออกมาจาก Core
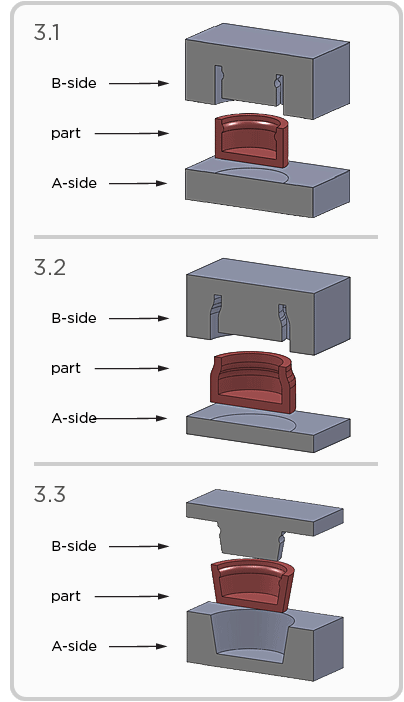
ซึ่งหัวใจของการออกแบบพลาสติกคือ จะต้องไม่มี Undercut เกิดขึ้น นั่นก็คือฉีดแล้วพลาสติกไม่ติดโมลล์ หรือเอาออกไม่ได้
เช่รูปที่ 1 ด้านในพาร์ทเป็นสลัก ทำให้ดึงไม่ออก
รูปสอง ติดมันทั้งด้านในและนอก
รูปสุดท้าย ติดด้านในเช่นกัน
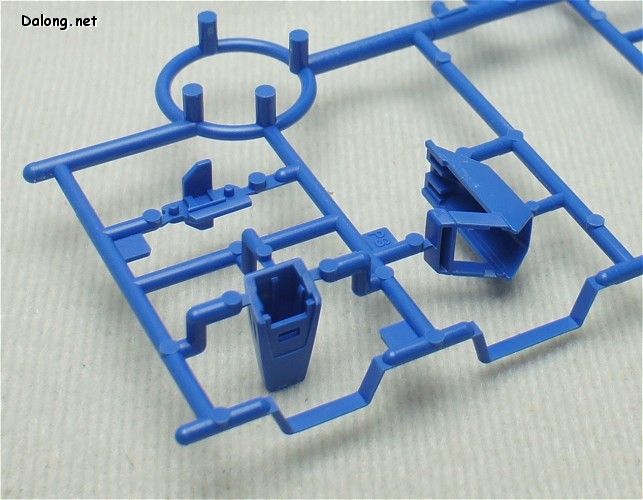
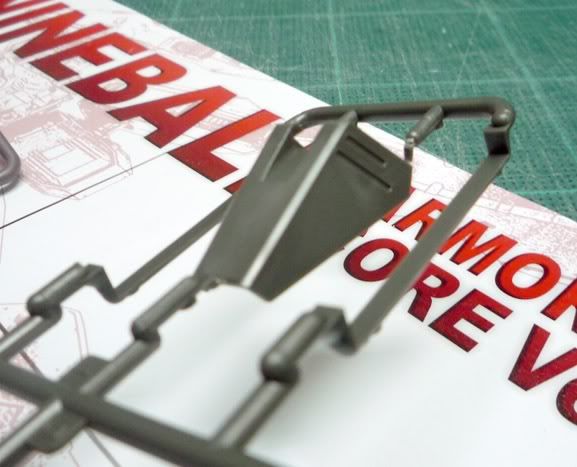
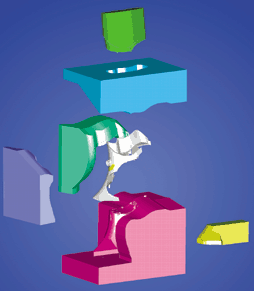
ซึ่งในกรณีที่จำเป็นจริงๆ สับหรับชิ้นส่วนที่ซับซ้อนมาก จะมีการเติมชิ้นส่วนของแม่พิมพ์เข้าไป นั้นก็คือ Slide core ก็คือจากกฐเดิมที่ว่าแม่พิมพ์ต้องมีสองซีก ก็จะมีซีกเล็กๆเพิ่มขึ้นมาตามแต่ความซับซ้อนของชิ้นส่วน บางชิ้นประกบซีกบนล่างซ้ายขวาก็มี
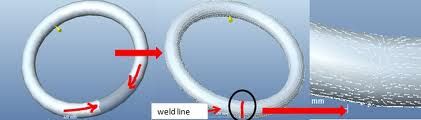
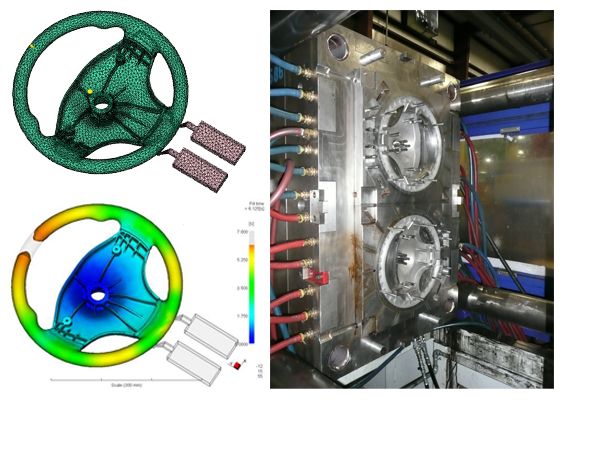
อีกอย่างที่จำเป็นก็คือ การจำลองการใหลของพลาสติก เช่นดังในรูป พลาสติกฉีดมาเข้าวงกลม แล้วมาเชื่อมตรงกลาง ทำให้ตรงกลางเชื่อมกันแบบหลวมๆ ทำให้มีโอกาศแตกได้ง่ายเพราะไม่ใช่เนื้อเดียวกันจริงๆ
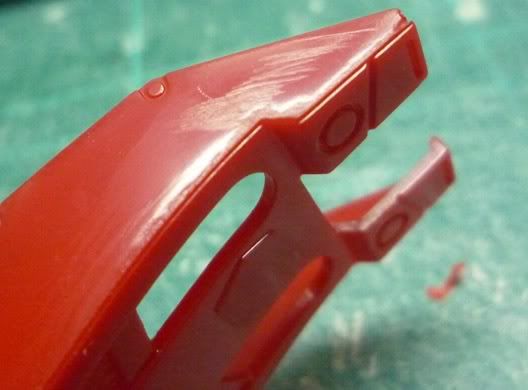
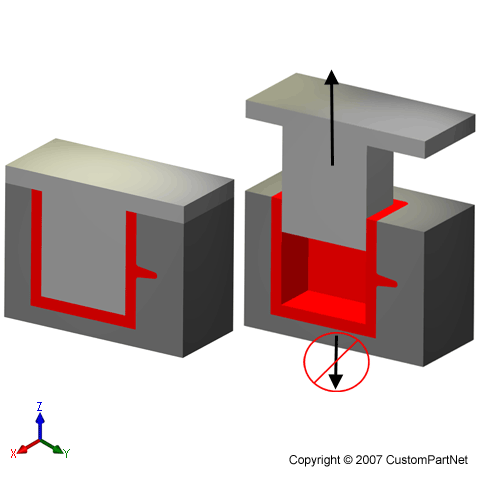
อีกส่วนนึงที่จำเป็นคือ การจำลองการถอดแม่พิมพ์
ดังที่เคยกล่าวในหัวข้อ Undercut ไปแล้ว ในกรณีนี้คือชิ้นส่วนพวกตรงๆ ถ้าตรงมากๆจะทำให้ถอดแม่พิมพ์ยากกว่าชิ้นส่วนที่มีความชัน ทางแก้คือไม่ทำชิ้นส่วนเวลาถอดแม่พิมพ์ให้ตรงพอดีเปะ ใส่องศาไปด้วยหน่อยๆเพื่อให้สามารถถอดแม่พิมพ์ได้อย่างใหลลื่น ไม่งั้นถอดแม่พิมพ์ไป ชิ้นส่วนขรูดกับโมลด์ไป
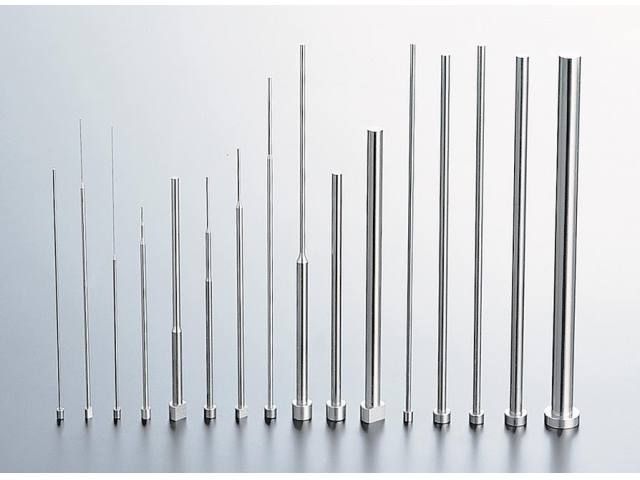
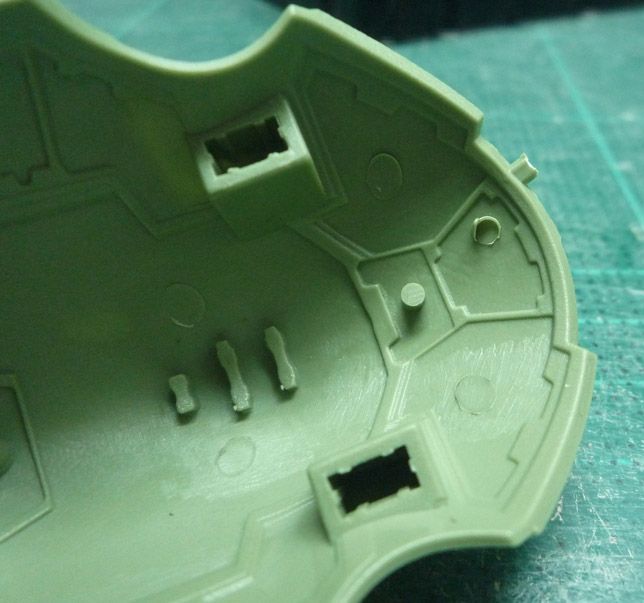
อีกส่วนนึงคือ Ejector pin นั่นก็คือเหล็กกระทุ้งดันชิ้นส่วนออกจากแม่พิมพ์นั่นเอง การวางออกแบบสำหรับพลาสติกโมเดลมักพยายามวางไม่ให้โดนส่วนที่โชว์ให้เห็น ถ้าพลิกมาด้านหลังเจอรอยกลมๆก็นั่นแหล่ะ
ซึ่งถ้าออกแบบมาไม่ได้ มันจะกินเนื้อพลาสติกไปเยอะ นั้่นคือออกแบบมาวางตำแหน่งไม่ดี
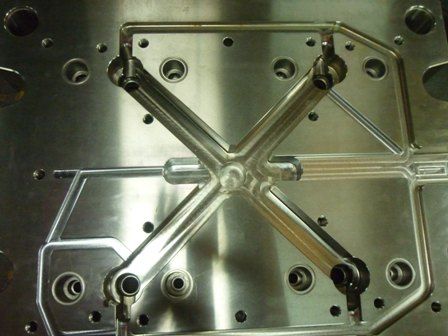
[/URL]
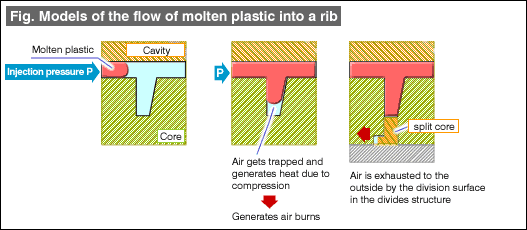
อีกส่วนที่สำคัญคือ จัดการทำ Air vent
เนื่องจากภายในแม่พิมพ์เป็นศูนย์ยากาศ แล้วเราอัดพลาสติกฉีดเข้าไป จึงจำเป็นต้องมีรูให้อากาศออก ไม่เช่นนั้นก็จะฉีดงานออกมาไม่สุด หรือเป็นรูโหว่เพราะไม่มีทางให้อากาศออก ซึ่งทางลมออกนั้นมักจะเล็กระดับไมครอน ทำให้เวลาฉีดพลาสติกไปแล้วพลาสติกไม่ใหลต่อไปตามรูเหล่านั้น
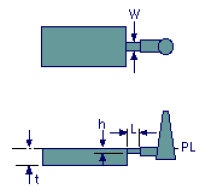
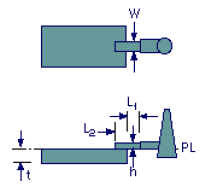
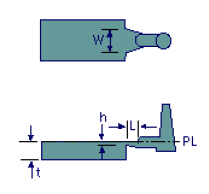
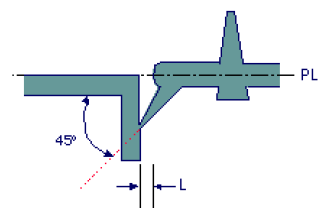
สุดท้ายที่คำคัญคือการออกแบบเกท ซึ่งอันนี้ก่อนอืนต้องเข้าโปรแกรมซิมูเลทการใหลก่อน
เช่น รูปที่สองของทุกบรรทัด จะเห็นว่าพลาสติกไม่ได้เข้าไปชิ้นงานตรงๆ เช่นรูปขา พลาสติกเวลาฉีดจะไป L2 ก่อน ก่อนที่จะม้วนลงไปด้านล่าง เป็นการฉีดแบบอ้อมๆเพื่อการกระจายตัว เพื่อแก้ปัญหาต่างๆ เช่นการฉีดพวกท่อกลมๆด้านบน หรือลดแรงประทะต่างๆ
ซึ่งเกทแต่ละแบบ มีคุณสมบัติพิเศษต่างๆกัน เช่น Submarine Gate, Pinpoint gate

ซึ่งเกทแบบ Pinpoint เท่าที่เคยผ่านตามามีแค่กระโปรง MG จิอองตัวเดียว คือเป็นเกทแบบเล็กมาก ฉีดออกมาแล้วจะสลัดเกททิ้งเอง
6. เริ่มทดลองฉีด หรือที่เรียกว่าเทสโมลด์ เพื่อตรวจสอบปัญหาต่างๆและแก้ไขก่อนการขายจริง
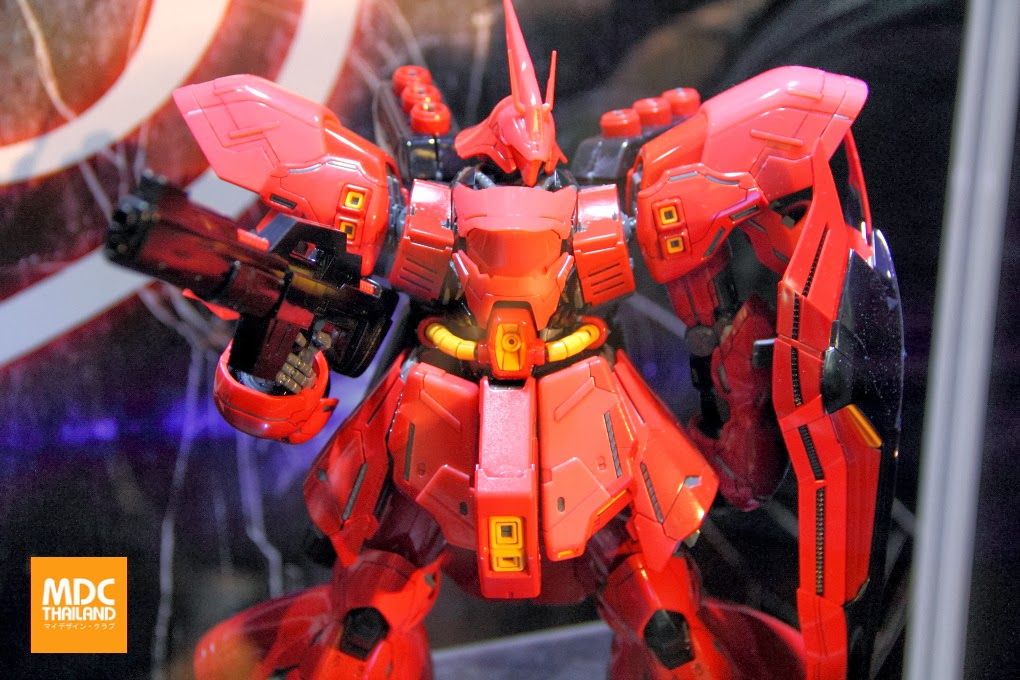
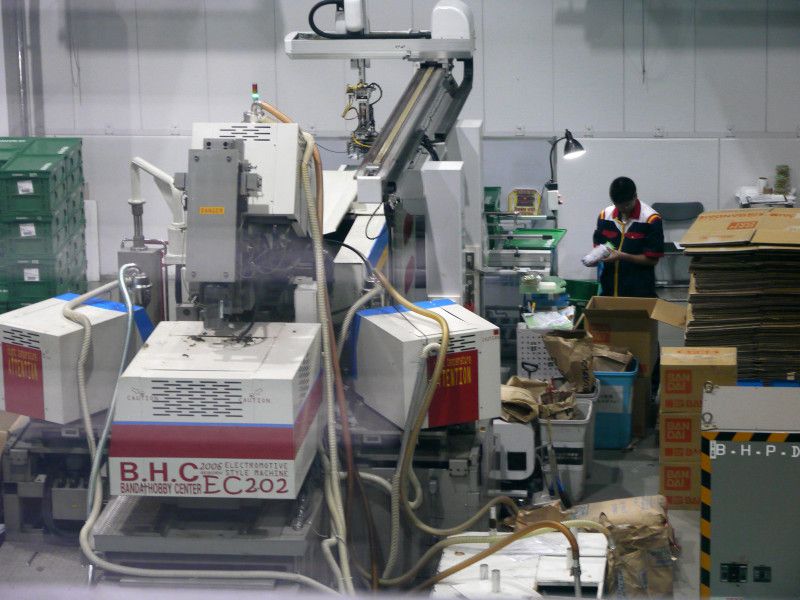
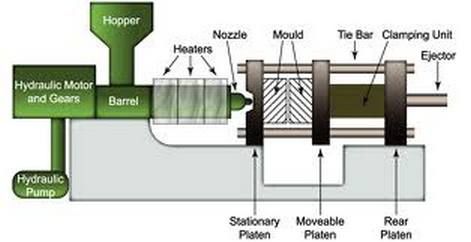
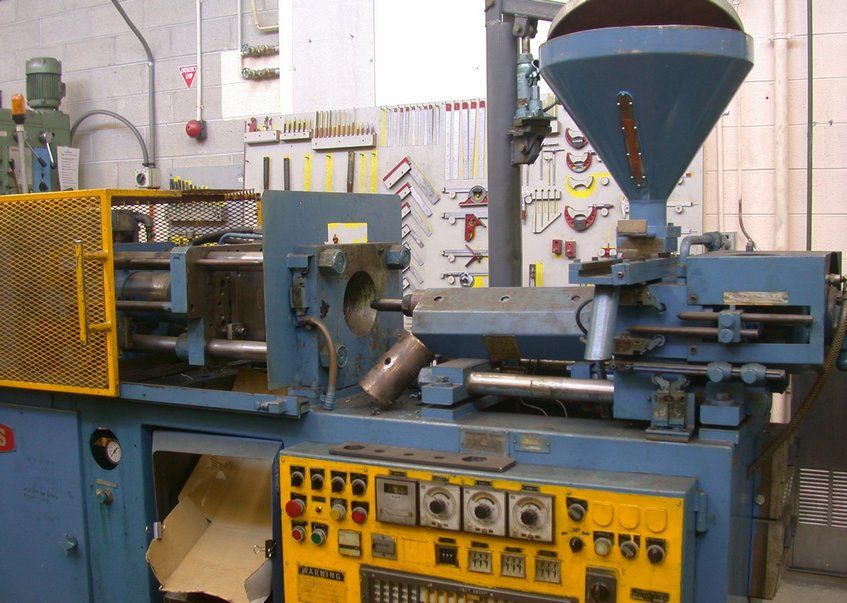
ซึ่งหลักการเครื่องฉีดพลาสติกแบบง่ายๆ ก็ได้แก่ถังใส่พลาสติก และเตาอบร้อนกับตัวสกรุที่หมุนเพื่อดันพลาสติกเข้าไปยังแม่พิมพ์ และหัวฉีดพลาสติก และกลไกเปิด-ปิด แม่พิมพ์
โดนเม็ดพลาสติกจะโดนใส่เข้าไปในแชมเบอร์ด้านบน และใหลเข้าไปสู่บาเรลติดฮีทเตอร์ ซึ่งฮีตเตอร์จะทำความร้อนในระดับที่อุณหภูมิที่สูงพอที่จะทำการละลายพลาสติกให้เหลวเป็นน้ำ
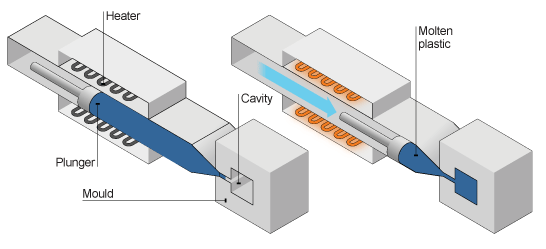
จากนั้นตัวสกรุด้านในบาเรลจะหมุนดันให้พลาสติกใหลเข้าสู่แม่พิมพ์ โดยตัวแม่พอมพ์เองก็โดนปรับอุณหภูมิด้วยเช่นกัน โดยในแม่พิมพ์จะมีการติดตั้งท่อฉีดน้ำร้อน ให้น้ำร้อนใหลไปในเหล็กแม่พิมพ์เพื่อรักษาอุณหภูมิแม่พิมพ์
ไม่เช่นนั้นแล้วทันทีที่ฉีดพลาสติกเข้าแม่พิมพ์ เหล็กที่เย็นจะทำให้พลาสติกแข็งตัวก่อนใหลเข้าไปในแม่พิมพ์จนสุด
ส่วนสำคัญของหลักการฉีดพลาสติกคือ
1. แรงดันแม่พิพม์ แม่พิมพ์ใหญ่มากแรงบีบก็ต้องมาก ไม่งั้นจะประกบไม่สนืททำให้เกิดครีบหรือหล่อเกินมาเยอะ
2. อุณหภูมิหัวฉีด ถ้าน้อยอาจฉีดไม่เต็ม
3. แรงดันหัวฉีด ไม่แรงอาจฉีดไม่สุด
4. อุณหภูมิแม่พิมพ์ ดังที่บ่นด้านบน
5. เวลาปิดแม่พิมพ์ ช่วงเวลาที่มให้พลาสติกแข็งคาแม่พิมพ์
6. เวลาในการฉีดแต่ละครั้ง สัมพันธ์กับด้านบนทั้งหมด
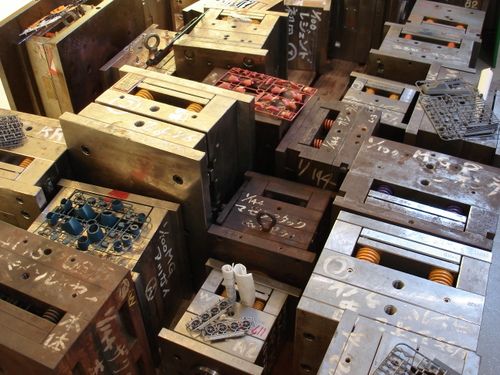
ซึ่งตัวแม่พิมพ์นั้นก็มีหลายขนาด หลายไซส์ ตามแต่ขนาดชิ้นส่วน ซึ่งแน่อนว่ายิ่งใหญ่ก็ยิ่งหนัก และฉีดยากขึ้น และขั้นตอนของการเปิด-ปิด แม่พิมพ์ก็ยิ่งต้องใช้แรงมากขึ้น พวกชิ้นแม่พิมพ์ใหญ่ๆเลยต้องคู่กับเครื่องฉีดที่ขนาดใหญ่ขึ้นเป็นเงาตามตัว
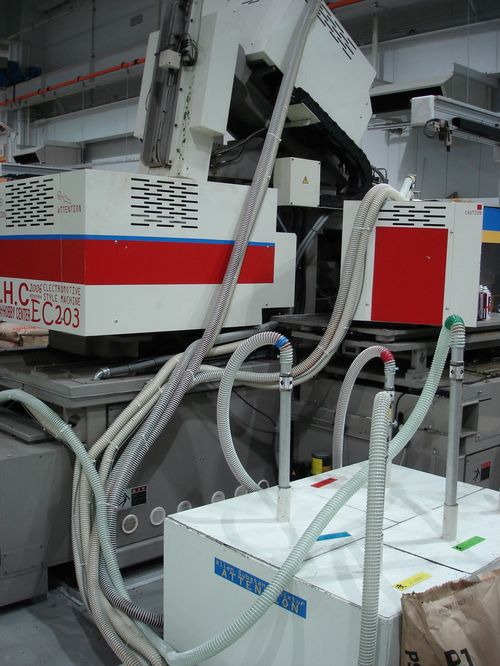
ซึ่งธรรมดาตามเครื่องฉีด พวกที่เก็บวัศดุพลาสติก จะมีเตาอบ และอุปกรณ์กันความชื้น
ซึ่งเนื้อพลาสติกก่อนที่จะทำการเอาไปฉีดขึ้นงานนั้น จำเป็นอย่างยิ่งยวดที่จะต้องอบไล่ความชื้นไปก่อน เพราะถ้ามีความชื้นปนเปื้อนเข้ามา อาจจะเกิดปัญหาอื่นๆตามมา เช่น ฉีดไม่ได้ขนาด เพราะพอโดนความร้อนความชื้นจะโดนไล่ไป เป็นต้น
ซึ่งในขั้นตอนนี้ ถ้าออกแบบแม่พิมพ์หรือ 3D ไม่ดีจะทำให้เวลาฉีดเกิดปัญหาต่างๆ เช่น
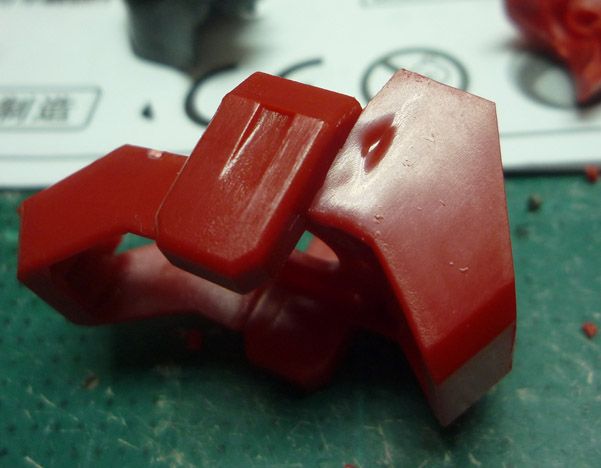
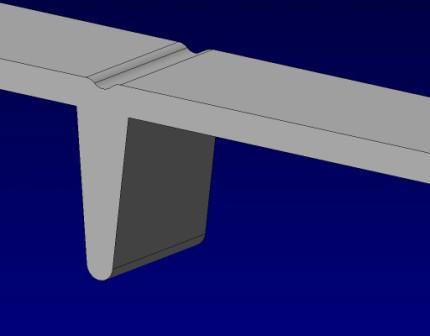
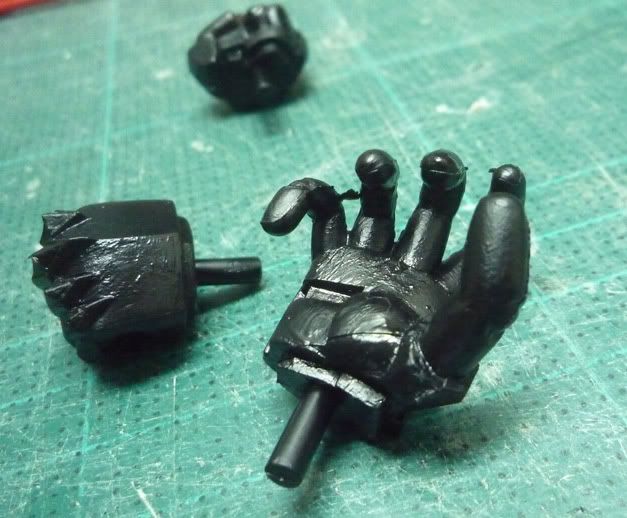
พลาสติกยุบ / ผิวเป็นรอย
มักเกิดจากการฉีดพลาสติกที่หนาเกิน ทำให้ผิวพลาสติกแข็งแต่ด้านในยังเป็นน้ำ พอด้านในแข็ง จากสภาพของเหลวสู่ของแข็ง ทำให้เกิดการหดตัวแล้วเกิดการดึงส่วนที่แข็งแล้วให้ยุบลงไปหรือเป็รอยย่น ดังรูป
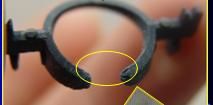
หล่อไม่สุด หรือฉีดออกมาแล้วมีรอยแหว่ง อาจเป็นเพราะเปิดรู Air vent ไม่พอทำให้มีอากาศอัดอยู่ฉีดไม่เข้า ไม่ก็ยังปรับอุณหภูมิไม่พอ
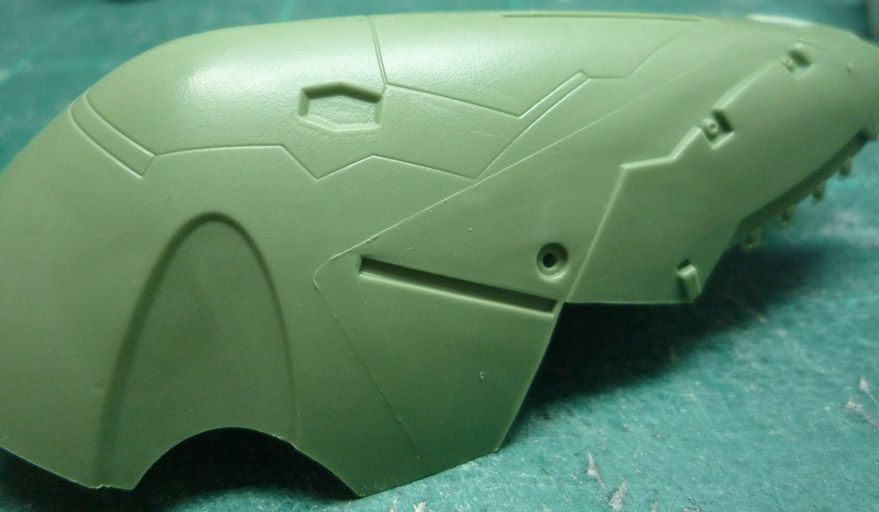
ตะเข็บหนา
อาจเป็นเพราะแรงดันทีอัดแม่พิมพ์เข้าด้วยกันไม่พอ ทำให้เวลาฉีดไปแล้วเลยทะลักออกมาตามขอบ
ไม่ก็ออกแบบแม่พิมพ์มาให้ประกบกันไม่ดีแต่แรก ไม่ก็ออกแบบแม่พิมพ์มาฉีดยาก เลยต้องอัดแรงดันให้พลาสติกยัดเข้าไปให้สุด แต่มันแรงมากไปเลยทะลักออกมาด้านรอยประกอบแม่พิมพ์ด้วย ไม่ก็เกิดการการใช้งานแม่พิมพ์ที่เกินอายุการใช้งาน เนื่องจากจังหวะ เปิด - ปิด แม่พิมพ์นั้นใช้แรงมาก ทำให้เหล็กมีอาการสึกหลอจากแรงอัดค่อนข้างแน่นอน ซึ่งใช้ไปนานๆจะสึกหลอ ทั้งนี้ทั้งนั้นขึ้นกับเกรดเหล็กที่เอามาทำแม่พิมพ์ด้วย
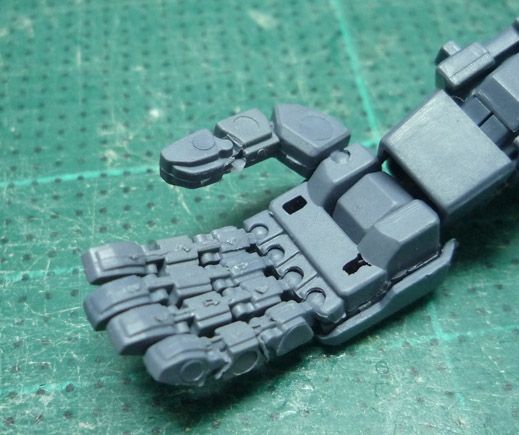
รอยเหล็กกระทุ้ง
วางตำแหน่งไม่ดีเลยกินเนื้อ ไม่ก็เกินเนื้อมามากเกินไป เกิดจากการวางตำแหน่งไม่ดี หรือชุ่ย หั่น/ตัน ปรับระยะก็หายแล้ว
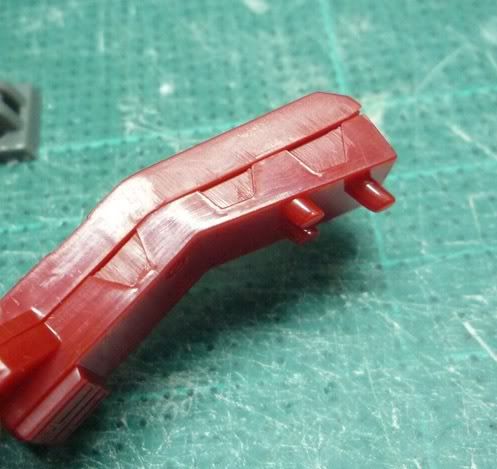
รอยถลอก เกิดจากการถอดโมลด์ยาก ดังด้านบนๆ
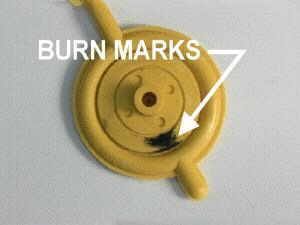
รอยใหม้
เกิดจากแก็สที่ค้างในแม่พิมพ์ออกไม่ได้ แต่โดนอัดมากๆก็เลยจุดไฟใหม้คาแม่พิมพ์ แก้โดยเปิด Air vent ไล่อากาศตามเดิม
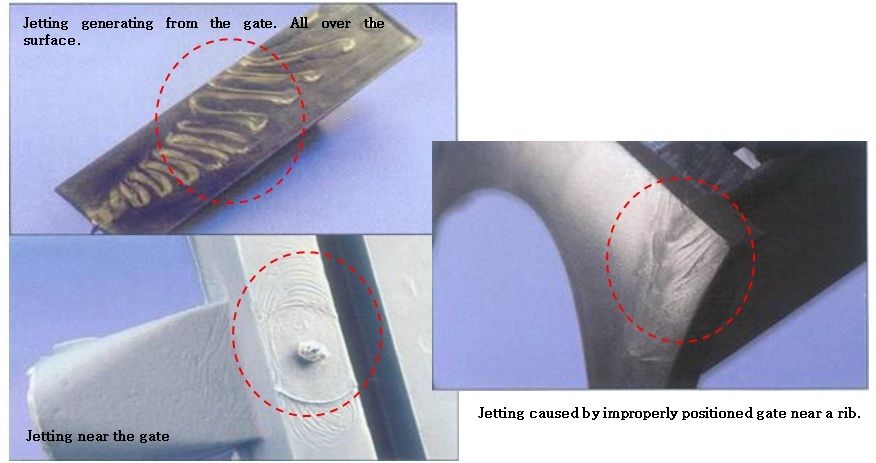
รอยฉีด
แรงดันมากไป เนื่องจากเกทนั้นตรงทำให้แรงดันอัดไปตรงๆ เปลี่ยนเกทไทป์ ซะเพื่อลดแรงกระแทก / แรงดันขณะฉีดพลาสติก ไม่ได้ฉีดเข้าชิ้นงานตรงๆ
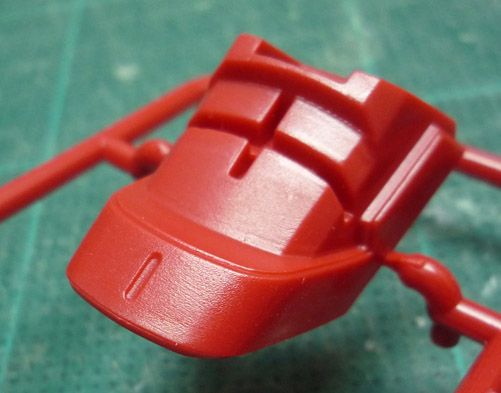
ผิวเป็นรอยไม่สม่ำเสมอ
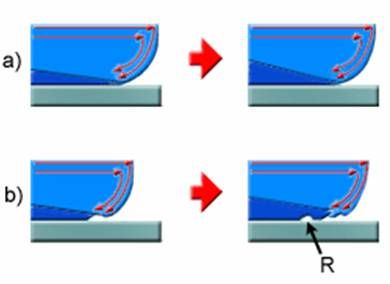
เกิดจากอุณหภูมิแม่พิมพ์น้อยไป
หลักการที่ควรคำนึงถึงเสมอของงานฉีดพลาสติกคือ 1. พลาสติกจะใหลไปที่ๆใหลง่ายก่อนเสมอ 2. ขณะฉีดพลาสติกจะเริ่มแข็งตัวตลอดเวลา
จากการที่อุณหภูมิฉีดน้อยไป หรือแม่พิมพ์เย็นเกิดไปทำให้พลาสติกเกิดการฉีดไป แข็งไป เลยใหลเป็นขั้นบันได ชั้นๆ ตะปุ่มตะปั่ม เพราะมันใหลไปสะดุดไป เลยออกมาผิวดูสะดุด
7. ตรวจสอบระบบการผลิต
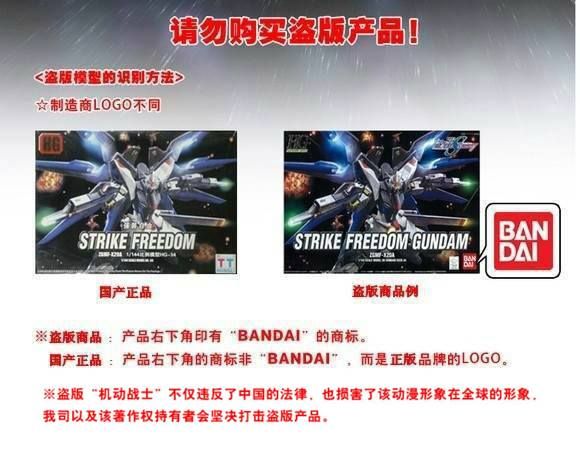
ในงานฉีดพลาสติก ต้องคำนึงถึงเสมอว่า งานฉีดพลาสติกมีค่าความคลาดเคลื่อนในการฉีดเสมอ
ซึ่งทั้งนั้ทั้งนั้นแล้วแต่เกรดของพลาสติกที่ฉีด
เช่น ABS อัดตราการหดตัวที่ 0.3-0.6%
PP ถ้าจำไม่ผิด (ขี้เกียดเปิดชีทดูละ) 1.6-2.6%
ซึ่งอย่างที่บอกว่าอุณหภูมิหัวฉีด และ ความชื้นในพลาสติกมีส่วนสำคัญมาก เพราะอุณภูมิทำให้วัศดุขยายตัว พอแข็งแล้วเลยหดมากเพราะที่ฉีดไปมันขนายตัวเพราะความร้อน ซึ่งความชิ้นในพลาสติกก็มีผลเช่นกัน
ฉะนั้น จึงทำให้งานบางล็อตได้มา อาจจะฝืด จะแน่น จะหลวมไม่เท่ากัน ตามการปรับอุณหภูมิเครื่องฉีด ซึ่งทั้งนี้ทั้งนั้นก็คือ การสุ่มเช็คตรวจคุณภาพของ QC นั่นเอง
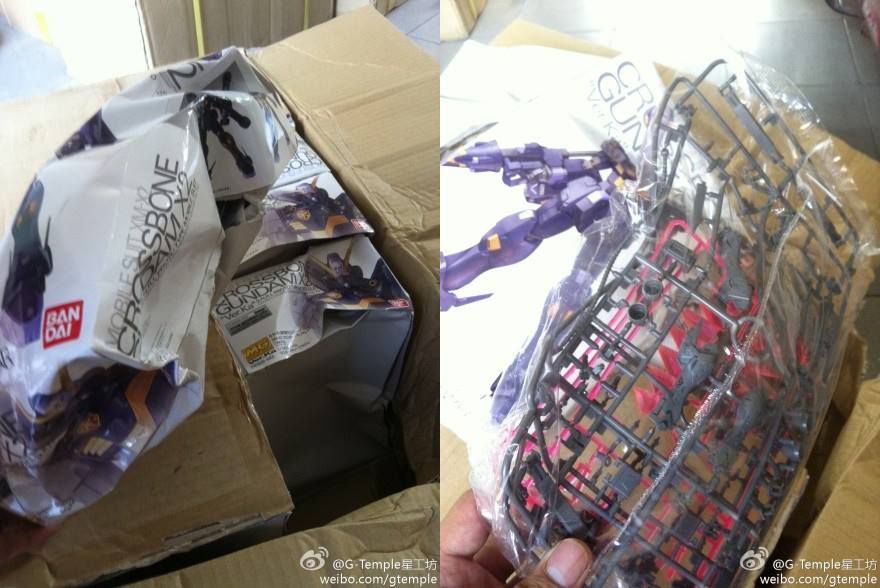
อีกหัวข้อนึงที่สำคัณไม่แพ้กัน นั่นก็คือการเทสระบบการขนส่ง
ถ้าไม่มีการเทสนี้เกิดขึ้น กว่าสินค้าจะมาถึงมือเราต้องผ่านรถขนส่ง ผ่านเรือ ผ่านไปรษณีย์ ถ้าไม่เช็คจุดนี้ดีๆกว่าจะถึงมือเราคงเละเสียก่อน
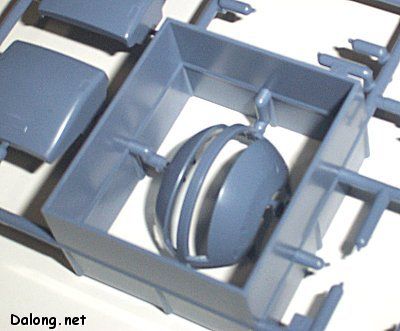
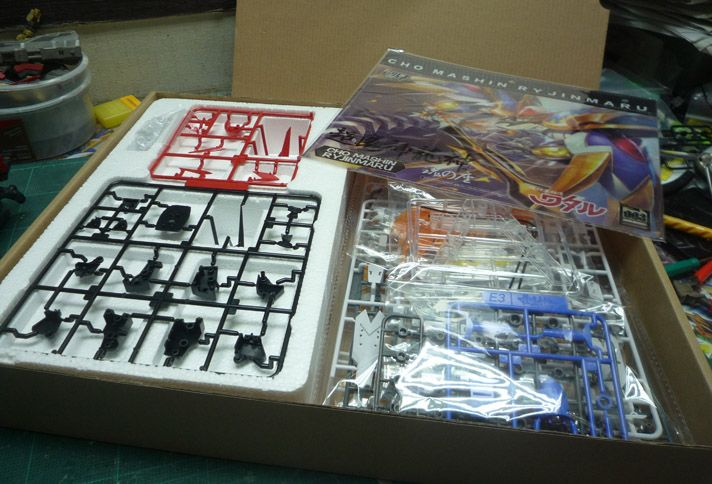
ซึ่งแต่ละคนก็มีวิธีป้องกันตนเองแบบต่างๆกันไป ใช้โฟมรองก็เจอมาแล้ว
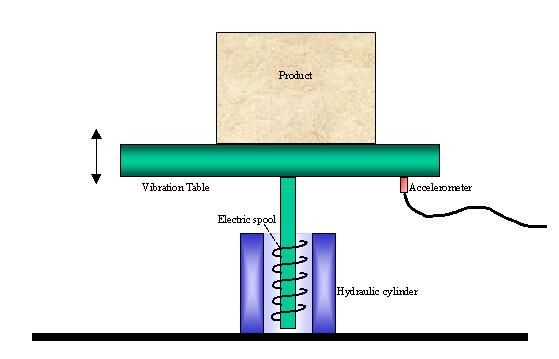
ซึ่งหัวข้อเทสที่แพร่หลายที่สุดคือ Vibration test เพื่อจำลองว่าลงเรือแล้วมันสั่ง มันจะรับแรงได้ใหม พลาสติกเขย่าไปมาจนหลุดจากแผงใหม หรือเสียดสีกันจนผิวเป็นรอยใหม
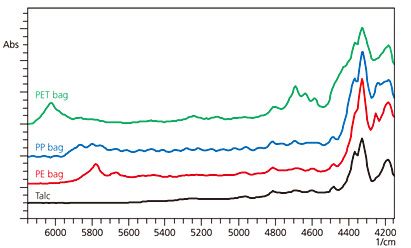
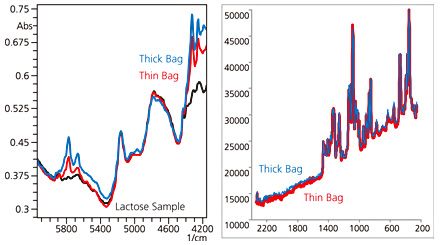
ซึ่งหลายๆคนอาจจะสงสัยว่าทำไมถุงลุงบันไดเฮียแกใช้สองแบบ คือถุบก็อบแกบ หรือที่เรียกว่าถุง PE และถึงพลาสติกเหนียวที่เรียกว่าถุง PP
ซึ่งถุงสองค่านี้ดูจากกราฟจะพบว่าค่าพารามิเตอร์ไม่เหมือกัน ส่วนตัวก็ว่าเกี่ยวกับการเทสน่ะแหล่ะ เพื่อใช้เลือกว่าจะใช้ถุงอะไร เรื่องราคาต้นทุนไม่แน่ใจเหมือนกัน
8. ทำการวางขาย รับทรัพย์กันไป
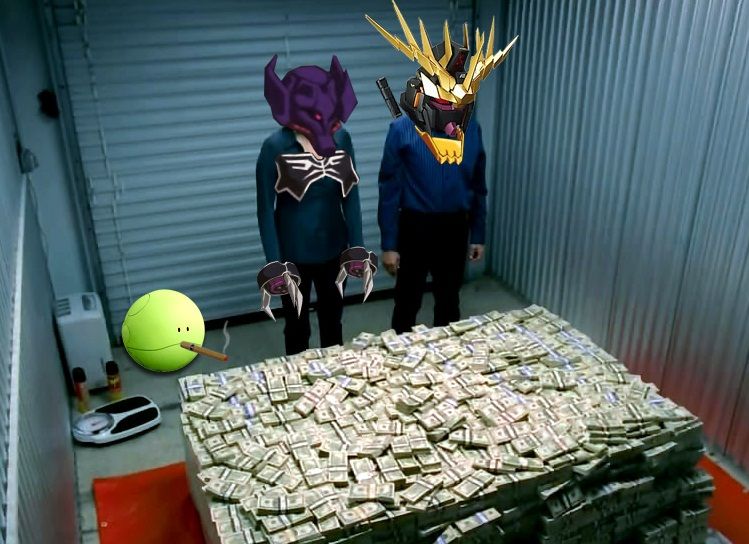
PS1. รูปเซอร์สเอาจาก Google ขอละการให้เครดิท
PS2. จากกระสบการณ์ส่วนตัวล้วนๆ อย่าเชื่ออะไรมาก
PS3. พิมพ์ผิดพิมพ์ถูกขออภัยล่วงหน้า
[youtube]http://www.youtube.com/watch?v=JL69zbcu6Qo[/youtube]